This article first appeared on GPNmag.com (Production June 2017)
_________
The best lighting applications are tailored to each production situation. Here are some common scenarios along with their best solutions.
Lighting plays an important role for both ornamental growers and controlled environment agriculture (CEA) growers. For ornamental crops, photoperiodic lighting controls flowering, while supplemental lighting increases light intensity to reduce crop time and improve crop quality. For CEA growers, lighting is critical to achieving consistent yield and product quality for year-round production.
While some lighting products bring flexibility for use in several different CEA applications, the best solution will be tailored to the production scenario. This article describes some common production scenarios and top choices for these situations. Before we get to specifics, it’s important to understand some basic terms and concepts.
Understanding Lighting Terms
Light quality refers to the colour, or wavelength, of light. Wavelength is described in nanometers (nm). All horticultural fixtures focus on photosynthetically active radiation (PAR), or light in the 400-700 nm range. Light quality varies with fixture type. High-pressure sodium (HPS) fixtures provide full-spectrum light, with heavier representation of middle wavelengths (green, yellow) and red/far red light. This light appears yellowish in colour. Metal halide (MH) fixtures also provide full-spectrum light, but with more blue and less red and far red than HPS. This heavier percentage of blue light tends to reduce stem elongation and impacts production of secondary compounds (e.g., improved anthocyanin production for leaf colour). Light from MH fixtures does appear bluer in colour. Light-emitting diode (LED) fixtures can provide true white light, full-spectrum light or very narrow-spectrum light, depending on the diodes used. Recipe-specific standard options typically include white, blue, red and far red light in varied proportions. Some LEDs are easily recognized by their pinkish light, but remember that the human-perceived colour can differ greatly depending on diode use.
Light intensity is the energy, or strength, of light. Our industry describes light intensity in several ways, which can lead to some confusion. First, the standard unit of measurement for light energy (intensity) is the micromole (μmol). Next, some descriptors of intensity refer to light generated by the fixture, while other descriptors refer to the intensity of light striking a surface. Photosynthetic photon flux (PPF), measured as μmol/s (s=second), describes an instantaneous measure of light intensity produced by a fixture. However, fixtures vary greatly in how this light is directed. Some fixtures have a more focused dispersal pattern and some have a wider dispersal pattern. The photosynthetic photon flux density (PPFD) considers both fixture output and dispersal. PPFD describes light intensity delivered to a surface and is measured as μmol/ m2/s (micromoles of light hitting a square meter in one second). PPFD is also an instantaneous measure of light intensity. Remember that the PPFD reported for a fixture is specific to the distance at which the measurement is taken.
Daily Light Integral
Instantaneous intensity measures like PPF and PPFD help us to compare fixtures, but when we reference crop needs, we need to consider the cumulative light delivered to the crop over the entire light period. Enter the daily light integral (DLI). DLI is measured as mol/m2/day (1 mol = 1,000,000 μmol). Fixtures with different PPFD can be used to achieve the same DLI by adjusting the distance from the crop and the duration of fixture operation.
Efficiency
Growers also should consider efficiency in fixture operation: How much light does a fixture create for each unit of energy consumed? In this case, the unit of energy most often used for comparison is the joule, with the efficiency rating reported as μmol/J (if you think in terms of power, i.e., watts, 1 W = 1 J/s). Remember that μmol/J relates only to the cost of operation and does not consider how the light hits the crop.
How the light hits the crop, the uniformity, is the last consideration. Uniformity can be good or poor with any fixture and is driven by the installation. Specifically, uniformity is impacted by the fixture dispersal pattern, the spacing of the fixtures and height at which they are installed. A well- developed light plan will deliver a uniform PPFD to the crop across the production space. Be careful about focusing solely on the average PPFD over a production space; also consider the difference between the high and low intensity areas over the crop.
A Grower’s Guide to CEA Lighting
How do some light fixtures stack up? We’ve compiled key descriptors here to help you compare and contrast. Contact your supplier for recommendations regarding lighting strategies that will work best for your specific needs.
Common Crop Scenarios
With the above basic knowledge in place, let’s address some common crop scenarios. Keep in mind that every situation is different and each production scenario will have slight differences. However, some commonalities do hold true.
Greenhouse high wire crops
For tomatoes, peppers and cucumbers that require supplemental lighting in the greenhouse environment, the idea is to simply supplement the natural light with high-intensity fixtures to increase DLI. DLI targets vary by crop. Michigan State University lighting expert Roberto Lopez suggests 30 mol/m2/d or higher for tomatoes or peppers and about 20 mol/m2/d for cucumbers.
These crops are traditionally lit with HPS fixtures. However, we’re also beginning to see increased use of LEDs. If choosing LEDs, select full-spectrum options with a dispersal pattern suited for greenhouse use. Intra-crop lighting (ICL) fixtures are positioned so that they are located within the canopy as the crop grows. The goal is to provide PAR to the shaded, lower part of the crop. Research data indicate benefits from ICL in some situations. Another good idea: Consider light-diffusing greenhouse coverings. These coverings essentially spread the light more efficiently through the greenhouse, so that more of the light finds its way to the crop.
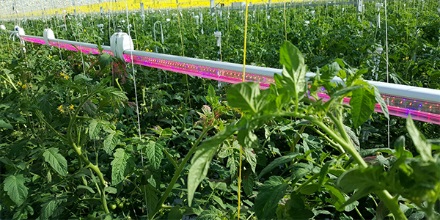
Greenhouse leafy greens
If the goal is simply to increase DLI in the greenhouse, then high intensity HPS, MH and full-spectrum LEDs are all useful. Lopez suggests targeting 12-13 mol/m2/d for lettuce crops, though slightly higher levels are beneficial. This is not a case where “if a little is good, a lot more is better:” Lettuce will develop tip burn under high light, which Lopez reports after three days at 17 mol/m2/d.
LEDs offer several benefits. First, they produce less waste heat, which reduces heat load on the crop. Second, LEDs allow narrow- spectrum treatments to develop red leaf color in some lettuce varieties following relatively short treatments (higher blue light enhances anthocyanin production). For crops that move through the production area, install the narrow-spectrum fixtures to treat the crop at the end of the cycle, shortly before shipping.
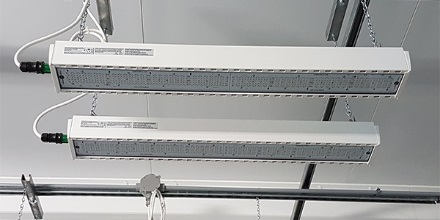
Warehouse herbs
Lower-intensity LED light bars are great choices for the tiered production systems most often used for plant factory production of herbs and leafy greens. These fixtures generate less heat, allowing crops to get closer to the lights without risk of damage, and reduce HVAC needs. Mounting height for these lower intensity fixtures will have a dramatic impact on the amount of light delivered to the crop. Always follow the recommendations from the supplier to ensure that adequate light is delivered to the crop in a uniform manner. Remember that non-uniformity in light will result in a non-uniform crop, so avoid trying to stretch your fixture count. The losses in crop uniformity and quality will far outweigh any savings in fixture costs. Once again, light quality can be manipulated to impact crop quality, including pigmentation, internode length and leaf size.
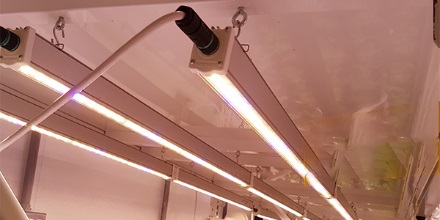
Warehouse medicinal crops
Propagation and early growth requires lower PPFD and can be managed with LED light bars, T5 LEDs/ fluorescents and dimmable LEDs. However, when it comes to flowering and finishing, high intensity LEDs are the obvious choice to provide high DLI while minimizing HVAC needs. Even with the advantages offered by LEDs, HPS fixtures are also commonly used. Regardless of the fixture type, intensity needs are very high for these crops. It’s not uncommon to target 400-500 μmol/m2/s for early growth and 900+ μmol/m2/s for mature crop phases.
While lighting technology can seem complicated, a basic understanding will help you evaluate your options. From there, your supplier can help you build a tailored solution for your needs.
Written by – Tami Van Gaal is CEA division leader for Griffin. She can be reached at tvangaal@griffinmail.com.